Tecnologia transforma casca de arroz em sílica sem geração de efluentes
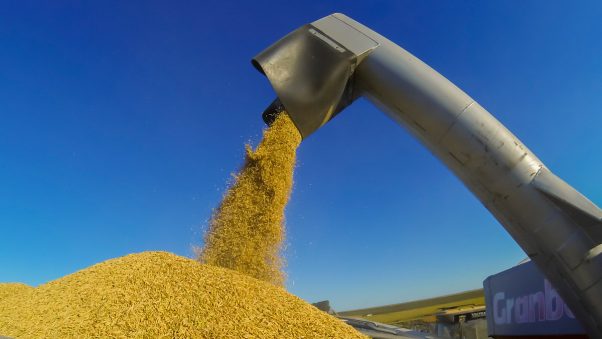
A Oryzasil, empresa do grupo alemão Ferrostaal, inaugurou em maio, em Itaqui-RS, uma unidade de produção combinada de sílica verde e energia, com base na queima de cascas de arroz. A instalação pode processar 20 toneladas por hora de cascas, gerando 2,5 mil t/mês de sílica e energia (térmica e elétrica) equivalente ao consumo de uma cidade com 200 mil habitantes. Tudo isso sem dar origem a efluentes.
A tecnologia aplicada na unidade de Itaqui foi desenvolvida pela Ferrostaal que, antes desse empreendimento, construiu a usina termelétrica UTE São Borja-RS, alimentada com biomassa proveniente do beneficiamento do arroz. O Rio Grande do Sul produz cerca de 70% do arroz brasileiro e Itaqui é a segunda maior região produtora do cereal no estado.
A Ferrostaal testou a geração integrada de químicos e energia na unidade piloto de Meleiro-SC. A produção combinada de energia e sílica é inovadora e exigiu estudos, realizados desde 2015.
Depois de Itaqui, a Oryzasil pretende instalar unidades similares em outras regiões do Brasil e do mundo, aproveitando diferentes biomassas. Segundo a companhia, a casca de arroz apresenta um teor médio de 20% de sílica ou dióxido de silício em sua composição. Outas plantas também acumulam a substância em sua estrutura, porém a casca de arroz é mais seletiva.
Na caldeira especialmente construída para o processo, a parte orgânica das cascas de arroz é queimada, liberando energia. A parte inorgânica forma as cinzas, ricas em silício, que reage com soda cáustica para dar origem ao silicato de sódio. Por sua vez, essa substância reage com ácido sulfúrico, resultando em sílica precipitada, sulfato de sódio (direcionado para a produção de sabões e detergentes) e um outro subproduto, utilizado como corretivo de acidez de solos agrícolas.
A sílica precipitada de origem natural, principal produto da Oryzasil, é apresentada em diferentes especificações, algumas delas com modificações de superfície, por exemplo, com silanos, para ser compatível com o substrato ao qual será adicionada. O produto pode ser aplicado a borrachas e pneus, creme dental, tintas e nos mercados de nutrição e saúde. “Também fabricamos sílicas de alta dispersibilidade e as linhas convencionais”, informou o CEO Albert Ramcke.
Como avaliou, “o processo da Oryzasil é competitivo por ter um ciclo de produção fechado, geramos nossa própria energia, livre de efluentes, pois recuperamos o co-produto sulfato de sódio enquanto o processo convencional o descarta, a água de evaporação dessa recuperação volta para o nosso processo”. Do ponto de vista ambiental, a unidade é muito positiva, por representar uma alternativa de aproveitamento das cascas de arroz, usualmente depositadas em aterros sanitários, onde geram metano e gás carbônico durante a sua decomposição. Em relação ao processo convencional de produção de sílica, a vantagem está em não depender da atividade mineradora de quartzo, que gera efluentes líquidos.
Consideramos que a escala da fábrica é adequada, uma das maiores da região, cuja capacidade instalada visa atender ao crescimento da demanda de sílica da região, principalmente do mercado de pneus verdes”, comentou Ramcke. “Se a demanda continuar crescente, o que depende do avanço da economia, uma nova fábrica na região dos Pampas pode ser pensada”, finalizou.
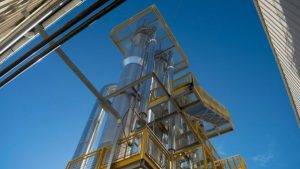
Tecnologia foi desenvolvida pela Ferrostaal
Material reproduzido de: Quimica.com.br